Non-Destructive Battery Inspection
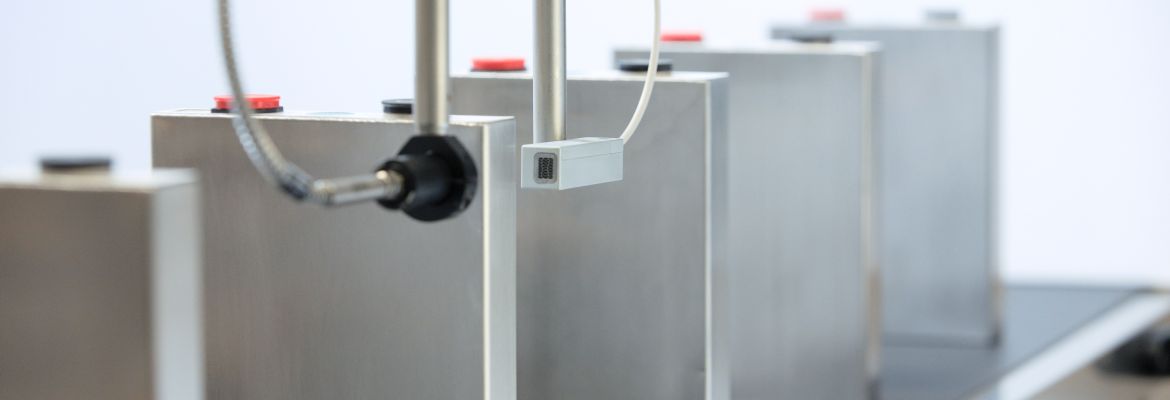
XARION's Battery Cell Ultrasound Inspection for the Battery Industry
XARION's LEA (Laser-Excited Acoustics) ultrasound NDT for batteries delivers quality control by utilizing non-contact ultrasound. Unlike conventional ultrasonic testing, XARION does not require any coupling agents or gels, offering a contact-free and fully automated solution.
This technology identifies properties that may significantly impact battery cell, module, and pack performance and lifespan. With the widespread use of batteries in applications such as electric vehicles, renewable energy systems, and electronic devices, ensuring battery safety, reliability, and performance is crucial by detecting and addressing potential issues early.
Features of XARION’s Battery Inspection Technology
- See inside the battery cell!
- Battery cell NDT, module, and pack inspection without contact or coupling liquid
- Fully automated and high-speed inspection
- Inspection of cells at all three stages: wetting, formation, and aging
- Ensuring perfect sealing of pouch cells
- Detecting void regions in thermal paste and gap filler in modules and packs from outside the housing
- Monitoring ultrasonic foil-to-tab welds in real-time
Ultrasound Inspection of Wetted, Formed, and Aged Cells
The full-surface and homogeneous wetting of battery cells with electrolyte fluid is a crucial factor for their lifetime and reliability. XARION's LEA ultrasonic technology enables the non-contact detection and assessment of wetting status within prismatic and pouch cells right after filling. The principle is shown in the image below: A short laser pulse creates an ultrasound wave within the battery, which travels through the cell. Locations that contain gas pockets or insufficient electrolyte wetting conduct less or no ultrasound, while sites that are well wetted or free of gas pockets conduct ultrasound. XARION's Optical Microphone detects the ultrasound leaving the battery cell, and the system’s software creates an image that allows you to see inside the battery cell. Furthermore, the system is ideally suited for performing fast, spatially-resolved battery cell NDT for formed and aged cells, detecting unwanted internal irregularities and precisely locating them within the cell.
Contactless in-line inspection during foil-to-tab welding and bus bar welding
Electrode foils are welded to current-collector tabs. This is crucial for the cell’s stability and safety and is done quickly and economically with ultrasonic welding machines. XARION’s Optical Microphone, in conjunction with the WeldAlyzer data analysis software, enables fast and reliable in-line process monitoring of this important battery production step.
Bus bars are used for permanent cell-to-cell and module-to-module connections. Laser-welding is often the method of choice, as it is a fast and cost-effective way of connecting bus bars. XARION's non-contact ultrasound inspection method enables the quality of these welds to be monitored, ensuring they meet performance standards and avoid failure after delivery.
Defect detection in pouch cell sealing
Unlike hard metal casings, pouch cells rely on a polymer-coated aluminum foil casing. Any errors in sealing these foils compromise the longevity of the pouch cell and can present significant safety risks. XARION’s battery NDT technology can automatically detect even the smallest leakages in pouch sealing, optimizing the production line's output and ensuring quality control.
Ultrasonic detection of thermal paste and gap fillers
To prevent overheating, all battery cells in a module or pack need to be thermally connected to the outer housing for effective cooling. This is typically achieved by filling any air gaps with a thermal interface material, thermal paste, thermal glue, or gap filler. XARION's contact-free, single-sided ultrasound inspection technique allows for fast and automated verification that all gaps are properly filled, ensuring a reliable thermal connection, even in large battery packs. Unlike X-ray imaging XARION's LEA technology does not struggle to detect even the thinnest delaminations effectively.
A direct comparison between XARION's LEA and X-ray/CT, revealed a key advantage of the XARION method. While X-ray/CT suggested merely the existence of thermal interface material in certain areas, XARION's technique accurately identified that no connection to the thermal paste in fact was present. This finding was confirmed via destructive testing. This level of precision makes XARION's solution a superior choice for ensuring the quality and reliability of proper thermal connections in battery systems.